Green Steel is an eco-friendly steel production method that uses renewable energy sources and recycled materials to reduce carbon emissions. Its importance lies in addressing environmental issues and promoting sustainable development.
Introduction to Green Steel
Green steel is important in the context of sustainable development because it has the potential to significantly reduce carbon emissions from the steel industry, which is one of the largest emitters of greenhouse gases. The traditional steelmaking process involves the use of coal and other fossil fuels, which emit large amounts of CO2. Green steel, on the other hand, uses low-carbon or zero-carbon technologies such as hydrogen direct reduction and molten oxide electrolysis to produce steel without emitting CO2.
By transitioning to green steel, the steel industry can significantly reduce its carbon footprint and contribute to global efforts to mitigate climate change. Additionally, the development and deployment of green steel technologies can create new economic opportunities and jobs in the renewable energy and clean technology sectors.
Green Steel Vs Traditional Steel Production
Green steel refers to steel that is produced using low-carbon or zero-carbon technologies, with the goal of reducing greenhouse gas emissions from the steel industry. Traditional steel production relies heavily on coal and other fossil fuels, which emit large amounts of CO2 during the production process. Green steel, on the other hand, uses alternative energy sources such as renewable electricity or hydrogen to power the steelmaking process, resulting in significantly lower emissions. This can be achieved through technologies such as hydrogen direct reduction (HDR) or molten oxide electrolysis.
Green steel production is still in its early stages but has the potential to significantly reduce the carbon footprint of the steel industry. Green Steel refers to the production of steel using low-carbon technologies that significantly reduce or eliminate greenhouse gas emissions. This includes technologies such as hydrogen direct reduction and molten oxide electrolysis, which use electricity instead of coking coal as the main energy input.
The goal of Green Steel is to decarbonize the steel industry and reduce its contribution to global greenhouse gas emissions.
Technologies for Green Steel Production
Some of the methods and technologies used in green steel production include hydrogen direct reduction (HDR) and molten oxide electrolysis (MOE), which are low-carbon primary steelmaking technologies. Carbon capture and storage (CCS) can also be applied to blast furnaces to reduce emissions. Additionally, increasing the use of electric arc furnaces (EAF) for steel production, which rely on recycled scrap steel, can reduce emissions. Renewable energy sources such as wind and solar power can also be used to power steel production, reducing the reliance on fossil fuels. However, these technologies are not yet commercially available at scale and require significant investment and development.
Also Read: Sustainability: India Launches Steel Scrap Recycling Policy – India CSR
Environmental Impact of traditional steel production
Traditional steel production, which involves the use of coal as a reagent to reduce iron ore to pig iron, is one of the largest emitters of CO2, contributing 6%–7% of global greenhouse gas emissions. The process of making steel and shaping it into useful geometries requires high temperatures and intensive energy consumption, which usually comes in the form of fossil fuels.
On top of that, the steelmaking process requires breaking the chemical bond in iron ore to get access to pure iron, a reaction that requires a reagent to bind with oxygen. Broadly speaking, in the last 2,000 years of steelmaking, that reagent has been coal, which generates CO2 as a by-product. Steelmaking is on track to consume 50% of the total remaining 1.5°C carbon budget by 2050. In addition to CO2 emissions, traditional steel production also contributes to other forms of pollution, such as air and water pollution.
The Benefits of Green Steel
Green steel offers several benefits, including:
- Reduced carbon emissions: Traditional steel production is a significant contributor to carbon emissions, accounting for up to 7% of global greenhouse gas emissions. Green steel production, on the other hand, can significantly reduce carbon emissions by using renewable energy sources, such as wind and solar power, and by recycling scrap steel instead of using raw materials.
- Reduced energy consumption: Traditional steel production is energy-intensive, requiring large amounts of fossil fuels to power the furnaces used in the process. Green steel production can reduce energy consumption by using more efficient production methods and renewable energy sources.
- Resource conservation: Green steel production reduces the reliance on virgin raw materials, such as iron ore and coal, by using scrap steel in the production process. This reduces the strain on natural resources and helps conserve them for future generations.
- Improved air and water quality: Traditional steel production can lead to air and water pollution due to the release of toxic gases and chemicals. Green steel production, with its focus on renewable energy and resource conservation, can help improve air and water quality and reduce the negative impacts on human health and the environment.
- Economic benefits: Green steel production can create new jobs in the renewable energy and recycling sectors, while also reducing dependence on imported fossil fuels. This can help support local economies and promote sustainable development.
Why is Green Steel important?
Green Steel is important because it has the potential to significantly reduce carbon emissions from the steel industry, which is one of the largest emitters of greenhouse gases. The traditional steelmaking process is highly energy-intensive and relies on fossil fuels, resulting in significant carbon emissions.
Green Steel, on the other hand, uses low-carbon or carbon-free energy sources, such as renewable electricity or hydrogen, to reduce the carbon footprint of steel production. This is crucial for achieving global climate goals and reducing the impact of climate change. Additionally, the development and adoption of Green Steel technologies can create new economic opportunities and jobs in the clean energy sector.
Green Steel for Sustainable Development
By adopting green steel production methods, the steel industry can make significant strides toward reducing its carbon footprint and promoting sustainable development.
Green steel can help address environmental issues and promote sustainable development in several ways:
- Reduced carbon emissions: Traditional steel production is a significant contributor to greenhouse gas emissions, but green steel production uses renewable energy sources like wind, solar, and hydropower, reducing carbon emissions.
- Efficient use of resources: Green steel production involves recycling scrap metal, reducing the need for virgin iron ore and other raw materials. This conserves resources and reduces waste.
- Local job creation: The production of green steel requires skilled labor and technological advancements, creating new employment opportunities in local communities.
- Circular economy: Green steel production is a part of the circular economy model that promotes sustainable production and consumption by reusing resources and minimizing waste.
- Reduced pollution: Traditional steel production generates significant amounts of air and water pollution, but green steel production uses cleaner technologies and processes to reduce pollution.
Green Steel Projects around the World
The HYBRIT project in Sweden is a joint venture between an iron ore producer, a steel manufacturer, and a power utility, with the aim of replacing one blast furnace with zero-carbon steel technology by 2030. The project uses hydrogen instead of coal to reduce iron ore into iron, which is then used to produce steel.
The Green Steel for Europe project is a European Union-funded initiative that aims to develop a fossil-free steel production process by 2030. The project involves a consortium of 12 partners from seven European countries, including steel producers, research institutes, and universities. The project will focus on developing new technologies for the production of green steel, such as hydrogen-based direct reduction and carbon capture and storage.
Other examples of green steel initiatives and projects around the world include:
- The H2 Green Steel project in Sweden aims to produce fossil-free steel using hydrogen produced from renewable energy sources.
- The SteelZero initiative is a global industry coalition that aims to achieve net-zero emissions in the steel sector by 2050.
- The Tata Steel Europe project in the Netherlands involves the use of hydrogen to reduce iron ore into iron, with the aim of producing green steel.
Promotion of Green Steel in India
The Ministry of Steel in India has set an ambitious target of net-zero emissions by 2070. To achieve this goal, they are taking steps to promote decarbonization in the steel industry, such as promoting energy and resource efficiency, renewable energy, and green hydrogen. They are also incentivizing the steel industry to reduce energy consumption and adopt the best available technologies. Through their efforts, they hope to raise awareness about the emerging market for green steel and encourage more companies to adopt sustainable practices in the steel industry.
The iron and steel sector is one of the major contributors to carbon emissions, as reported by the Ministry of Environment, Forest and Climate Change (MoEFCC) in India’s Biennial Update Reports (BURs) to the United Nations Framework Convention on Climate Change (UNFCCC).
The Ministry of Steel in India has set a net-zero target by 2070, and in the short term, they are focusing on promoting energy and resource efficiency, as well as renewable energy to reduce carbon emissions in the steel industry.
Steps were taken for promoting decarbonization in the steel industry
The Ministry of Steel has taken several steps to promote decarbonization in the steel industry. These include:
- Steel Scrap Recycling Policy, 2019: This policy enhances the availability of domestically generated scrap to reduce the consumption of coal in steel making.
- National Green Hydrogen Mission: The Ministry of New and Renewable Energy (MNRE) has announced the National Green Hydrogen Mission for green hydrogen production and usage. The steel sector has also been made a stakeholder in the Mission.
- Motor Vehicles Rules: The Motor Vehicles (Registration and Functions of Vehicles Scrapping Facility) Rules, 2021, shall increase the availability of scrap in the steel sector.
- National Solar Mission: The National Solar Mission launched by MNRE in January 2010 promotes the use of solar energy and helps reduce the emission of steel industry.
- Perform, Achieve and Trade (PAT) scheme: The PAT scheme, under the National Mission for Enhanced Energy Efficiency, incentivizes the steel industry to reduce energy consumption.
- Adoption of Best Available Technologies: The steel sector has adopted the Best Available Technologies (BAT) available globally, in the modernization & expansion projects.
- Implementation of Japan’s Model Projects for Energy Efficiency Improvement: Japan’s New Energy and Industrial Technology Development Organization (NEDO) Model Projects for Energy Efficiency Improvement have been implemented in steel plants.
India: Focus on raising awareness
The Ministry of Steel is also focusing on raising awareness among manufacturers about the emerging market for green steel. By doing so, they hope to encourage more companies to adopt sustainable practices in the steel industry.
The Climate Imperative for Green Steel
The production of steel has been a significant contributor to global greenhouse gas emissions, with a global footprint of 2.9 GtCO2 per year. With the sector on track to consume 50% of the remaining 1.5°C carbon budget by 2050, it is critical to find new low-carbon solutions for iron ore reduction. While efforts to increase recycling have been made, the production of primary steel using coal emits more CO2 than is acceptable to keep global warming below 1.5°C. Hydrogen-based direct reduction is one of the several promising options being explored.
The need to decarbonize the steel industry is critical to curb climate change. Hydrogen-based direct reduction is one of the promising low-carbon technologies being explored. While there are challenges associated with its implementation, the potential benefits of hydrogen-based steelmaking are significant. With continued research and investment, the steel industry can transition to a more sustainable and low-carbon future.
The Steelmaking Process
The steelmaking process can be broken down into three steps: reduction, transformation, and forming. In the first step, the oxygen in the iron ore is separated from the iron to produce pig iron. In the second step, pig iron is alloyed with other minerals to create a crude steel material. Finally, the steel is formed into the final shape that the customer will use. While all these steps are energy-intensive, the bulk of the CO2 emissions originates from iron ore reduction.
Decarbonizing the Steel Industry
To decarbonize the steel industry, it is crucial to distinguish between the three process steps and their objectives, despite the common practice of co-locating and integrating them. While the integration improves energy efficiency, it is not always necessary to cool an ingot of pig iron down for transport and then reheat it for transformation. An often-highlighted carbon emissions reduction strategy is to shift from blast furnace production to electric arc furnace production, but the two processes are not direct substitutes. The EAF process requires an already-reduced input material and cannot produce steel from iron ore. Increasing the use of the EAF process requires an increase in the supply of recycled scrap steel. However, there will not be sufficient scrap available to provide all the steel that the global economy will consume.
Low-Carbon Technologies
To curb climate change, the process of reducing iron ore to a product equivalent to pig iron is imperative. After decades of research, several technologies are beginning to approach commercial readiness. In addition to carbon capture and storage, the two most promising low-carbon technologies are molten oxide electrolysis and hydrogen direct reduction. Currently, neither of these options is commercially available at scale.
The Promise of Hydrogen-Based Steelmaking
The hydrogen-based direct reduction has the potential to revolutionize the steel industry by enabling low-carbon production of primary steel. The technology uses hydrogen to reduce iron oxide, resulting in the production of water vapor instead of CO2. While there are some challenges associated with hydrogen production and supply chain, hydrogen-based steelmaking can be a game-changer for the industry’s decarbonization efforts.
Example
Steel Industry Pivots Towards Sustainable ‘Green Steel’ Production
The global steel industry is shifting towards sustainable and low-carbon production methods, with a focus on producing “green steel” that uses renewable energy sources like hydrogen and electricity from renewable sources. The goal is to reduce carbon emissions and promote a more sustainable future. However, there are challenges to producing green steel at scale, including the high cost of renewable energy and the need for significant investments in new technologies and infrastructure. Nevertheless, the potential benefits of green steel are significant in mitigating the impact of climate change.
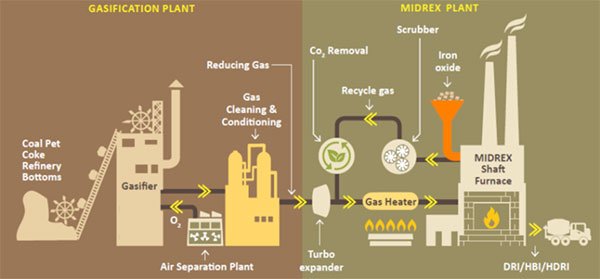
For example, Jindal Steel & Power Ltd. (JSPL), one of India’s leading steel manufacturers, has announced plans to produce “green steel” through a range of initiatives aimed at reducing its carbon footprint and promoting sustainable production.
JSPL has outlined several measures to achieve its goal of producing green steel. These include the use of hydrogen instead of coal in the direct reduction process, which produces steel from iron ore, as well as the adoption of carbon capture and storage technologies to reduce greenhouse gas emissions.
In addition, the company plans to set up a green hydrogen plant in Odisha, India, with a capacity of 500 megawatts. This plant will use renewable energy sources to produce hydrogen, which will then be used in the steel production process.
JSPL’s green steel initiatives are part of a wider trend in the global steel industry towards sustainable and low-carbon production methods. As concerns about climate change and environmental sustainability grow, many steel producers are investing in technologies and processes that reduce their carbon footprint and promote sustainable production.
However, there are challenges to producing green steel at scale, including the high cost of renewable energy and the need for significant investments in new technologies and infrastructure. JSPL and other steel producers will need to overcome these challenges if they are to successfully transition to a more sustainable and low-carbon future.
Despite these challenges, the potential benefits of green steel are significant. By reducing the carbon footprint of steel production, green steel can help to mitigate the impact of climate change and promote a more sustainable future. JSPL’s green steel initiatives are a positive step towards achieving this goal.
Challenges to Green Steel Adoption
The challenges facing the widespread adoption of green steel include high costs, limited availability of technology, and the need for a reliable supply chain of hydrogen generated by 100% renewables. The cost of hydrogen-based direct reduction and molten oxide electrolysis is currently 20%-30% higher compared to conventional steel production, which corresponds to a carbon price of around $70-$100/tCO2.
Additionally, the scale of change required is daunting, as the global economy consumes around 1,700 million tons of steel per year, and a 100-fold step-change in the pace of transition is needed for the steel industry to adhere to a 1.5°C pathway. However, as renewable power costs continue to plummet and new technologies enter the commercial pilot stage, low-carbon processes are starting to make economic sense.
Opportunities for Green Steel Innovation and Growth
The growing demand for sustainable steel production has opened up new opportunities for innovation and growth in the green steel industry. Governments around the world are offering incentives and funding to promote sustainable steel production. For example, the European Union’s Green Deal aims to make the continent carbon-neutral by 2050 and provides significant funding for green steel initiatives. Increased public awareness of the environmental impact of traditional steel production is also driving demand for green steel.
As a result, steel manufacturers are investing in new technologies and processes to reduce their carbon footprint, which could lead to significant growth in the green steel industry. Overall, the shift towards sustainable steel production presents a significant opportunity for innovation and growth in the industry.